Craftsmanship
Creating and shaping sunglasses
For more than forty years, we have been creating and shaping quality French frames. From the first sketches to the final wiping before shipping, they are completely made in our 1200m2 manufacture.
In a craft where every gesture is important, most operations require a great precision because they are carried out by hand. This craftsman approach is combined to current technologies. A balance is thus established in the well-preserved respect of a traditional know-how.
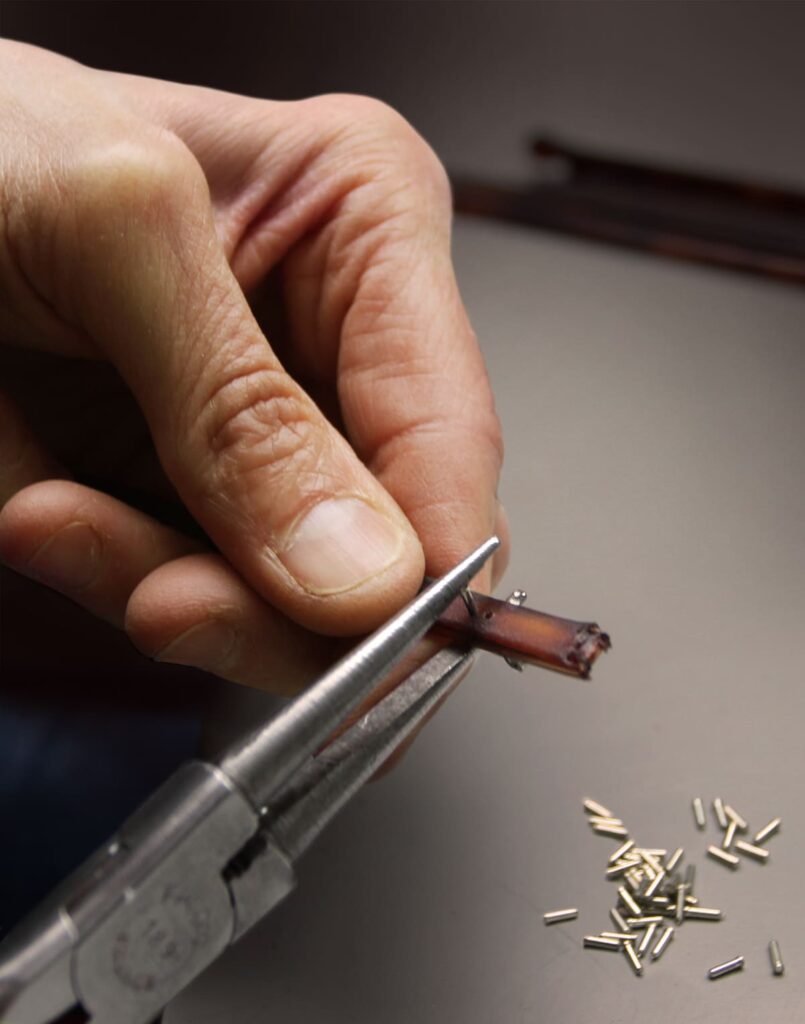
The material
Our meticulous work can be found as much in designing as in the choice of materials that we use to make our glasses.
They are made from sheets of cellulose acetate. It is a polymer which is three-quarters natural, made from a mix of cotton fiber and one fourth of a plasticizer. It is a material that we choose with great care from the world leader’s which is Italian. Cellulose acetate resists to mold and it is hypoallergenic.
The solar lenses are selected for their quality, they bring an optimal protection from the sun with a UV 400 ( CR39 lenses )
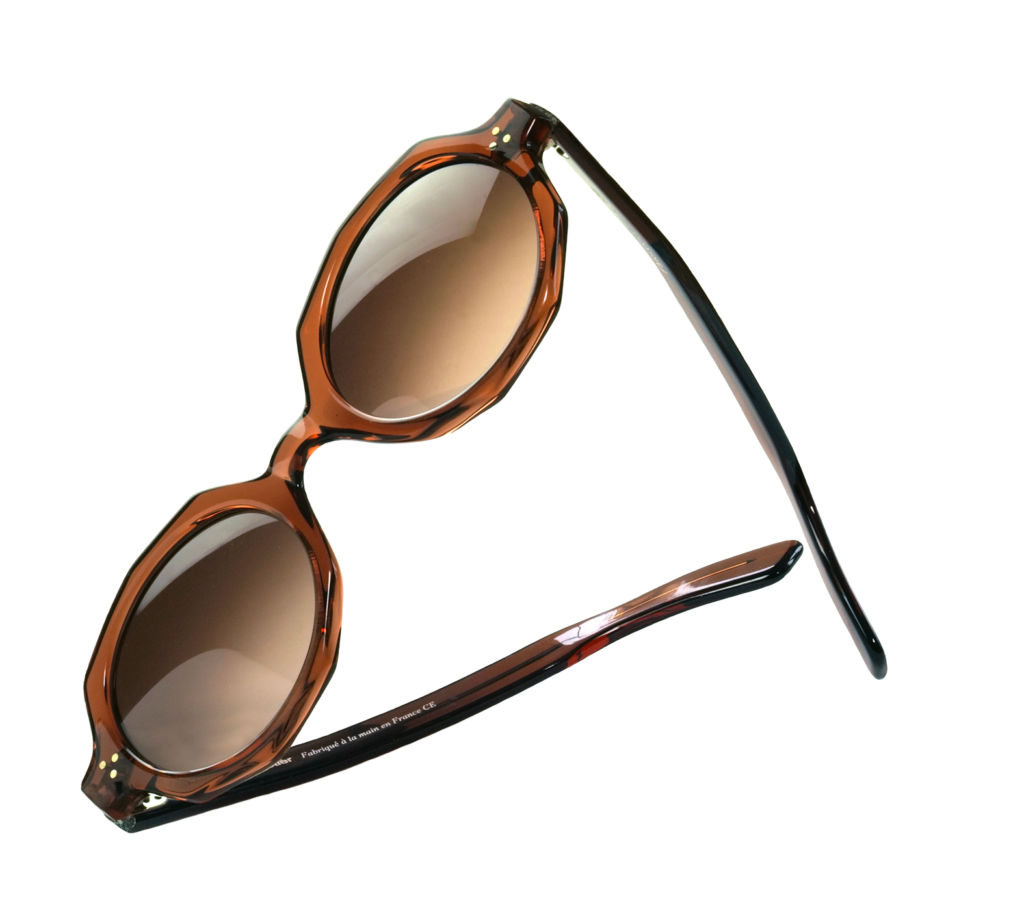
| Made in France
All of our frames have been creating and shaping in our family workshop in France. They all have the highlight certification “ French Origin Guaranteed ”.
| High quality and durability
Handcrafted sunglasses, with a traditional savoir-faire combined with recent technology to make quality products.
| Diversity of shapes and colors
A wide range of models, in very differents shapes but always offering quality at affordable prices.
Backstage in the workshop, in France
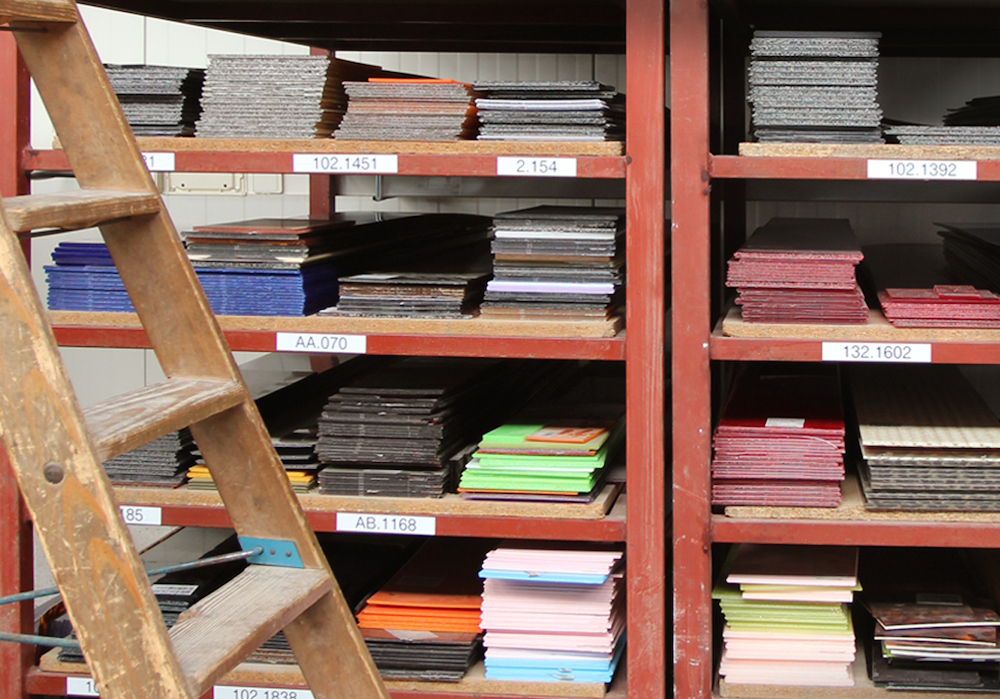
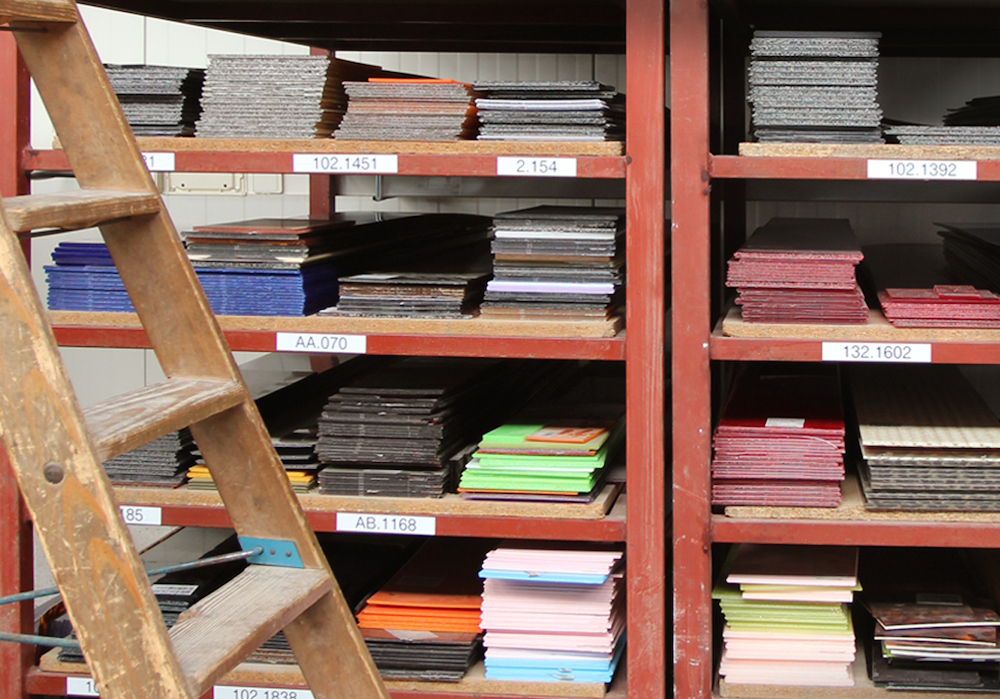
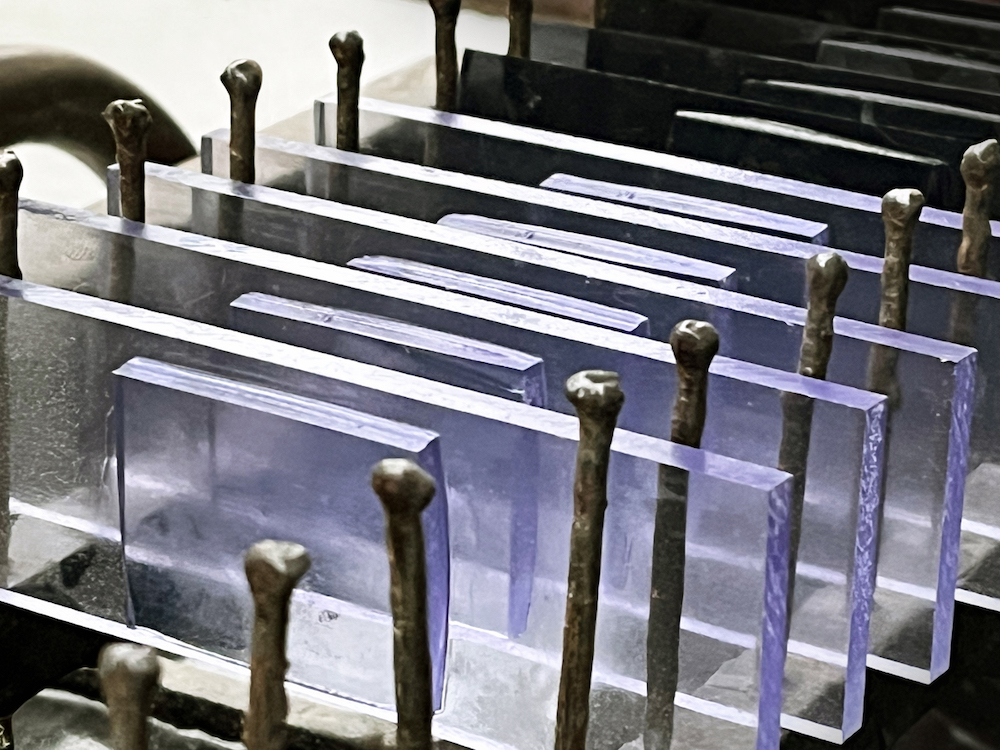
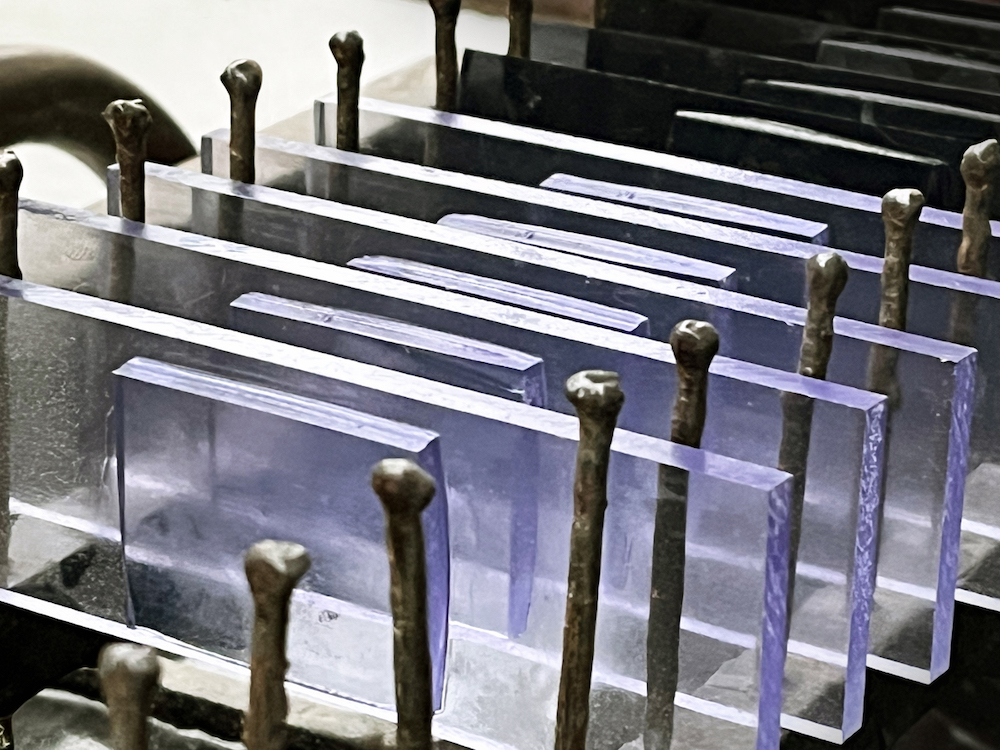
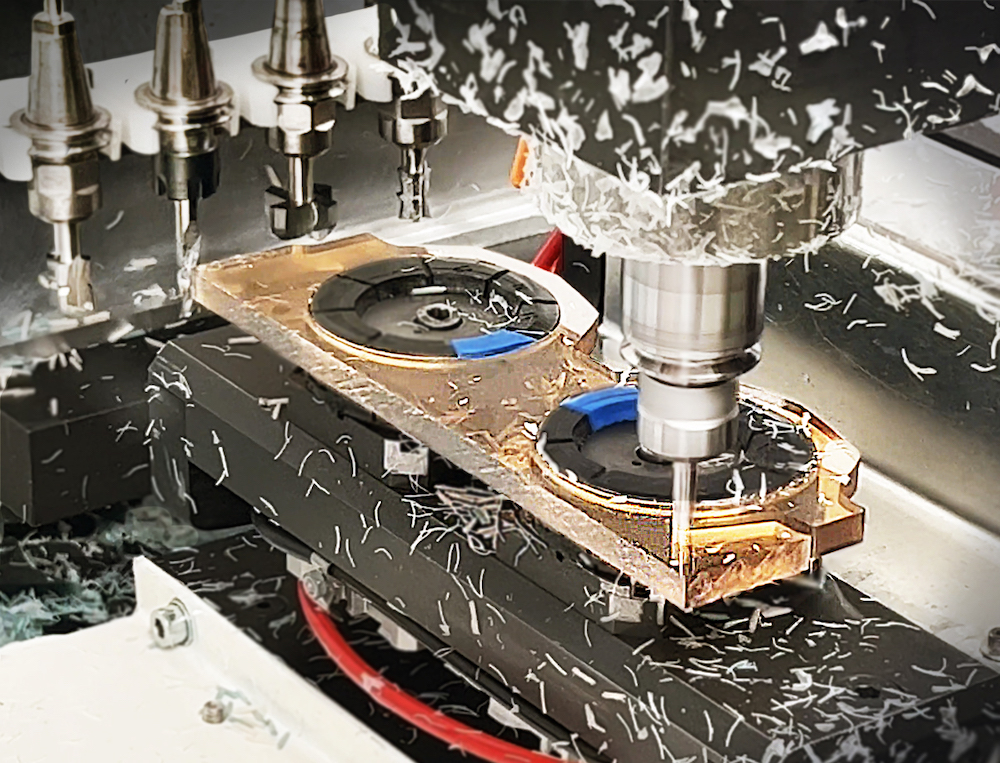
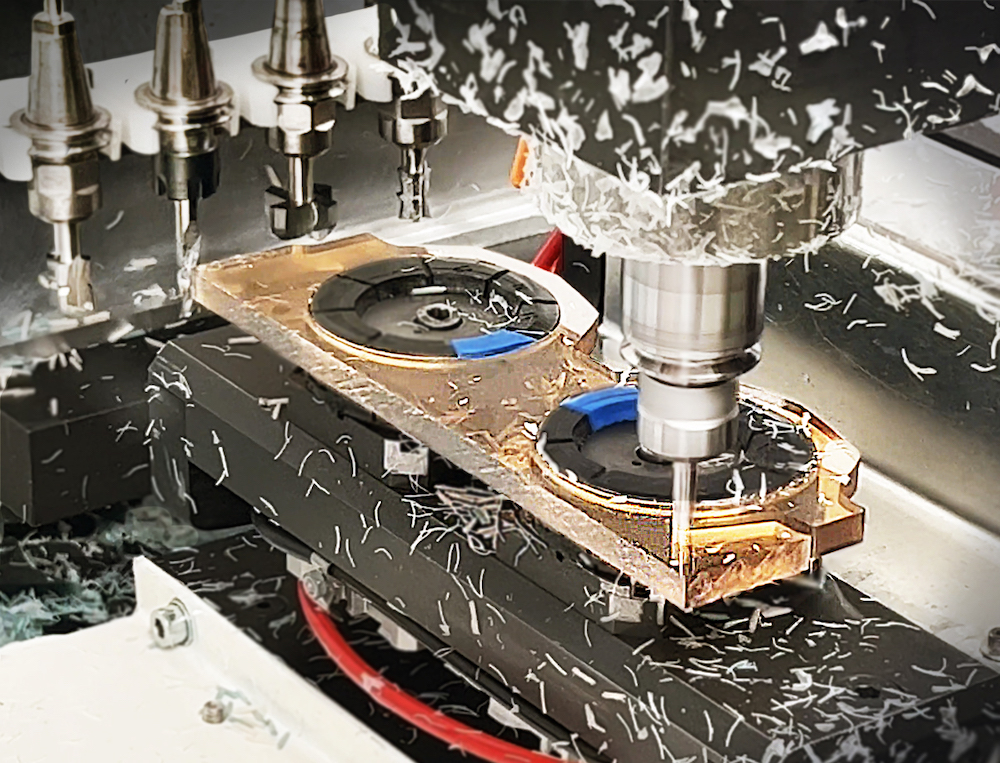
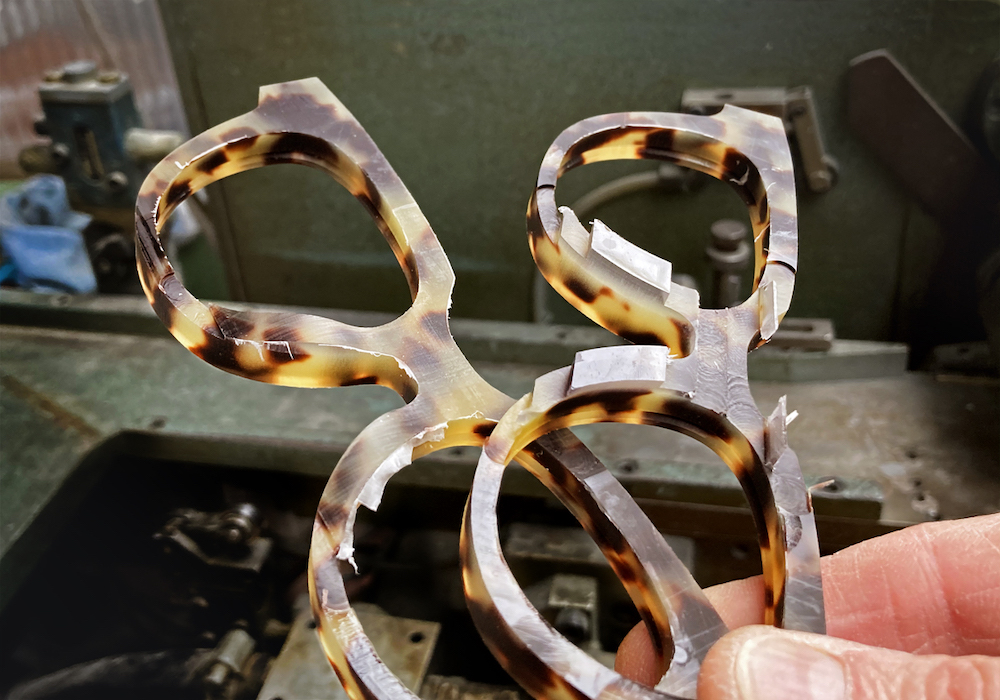
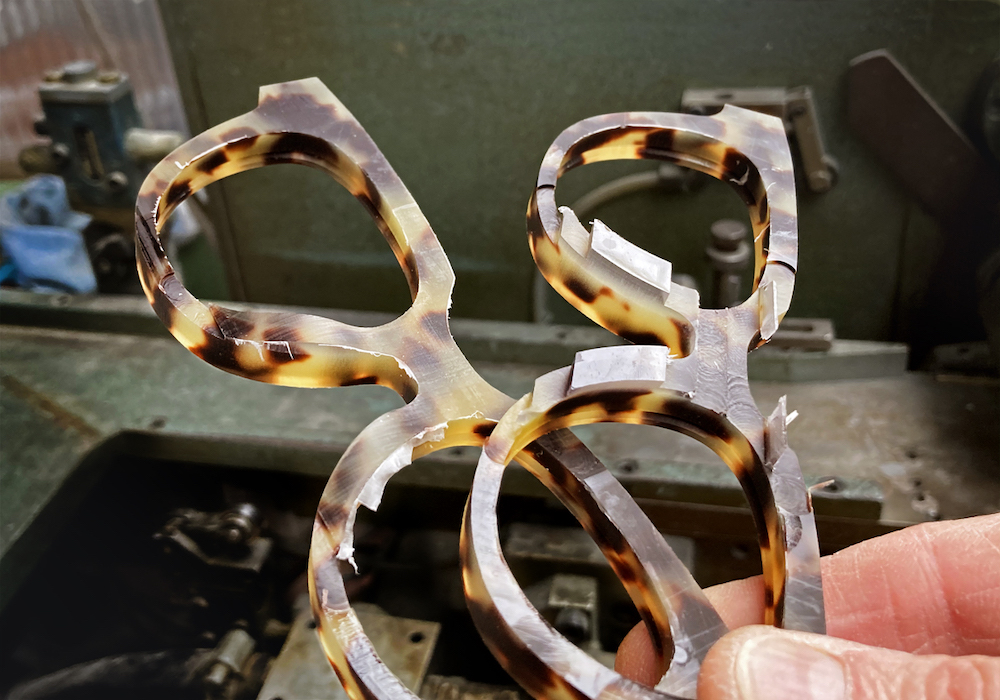
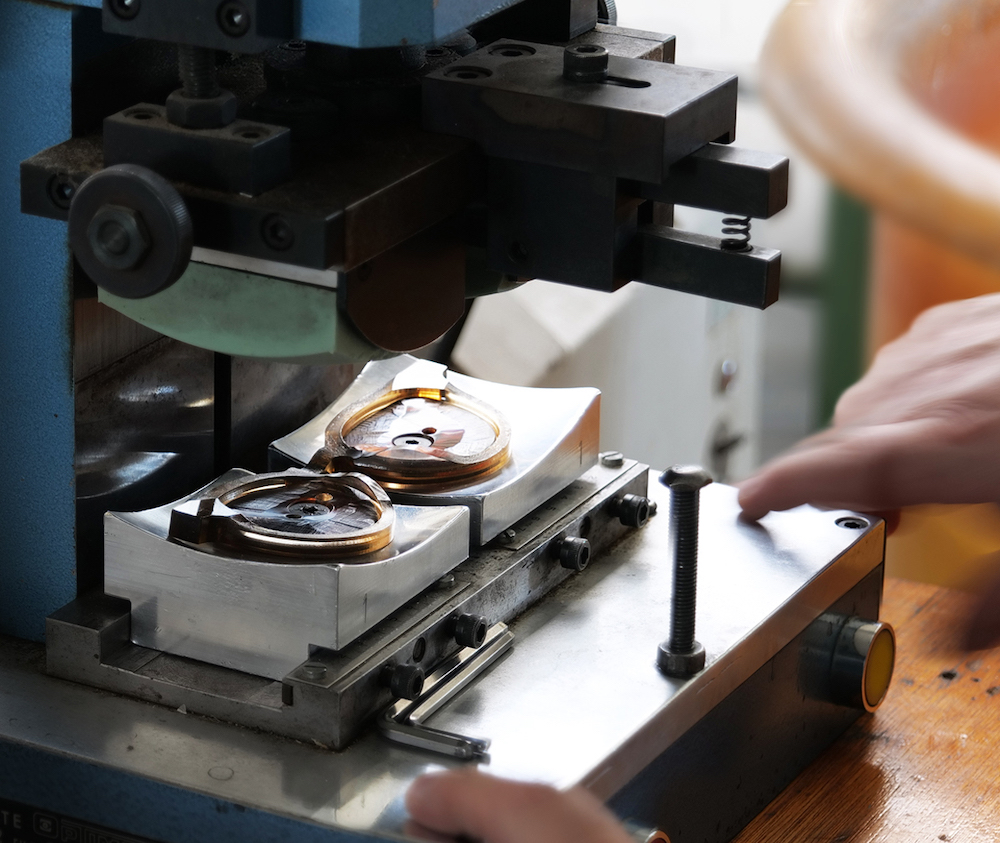
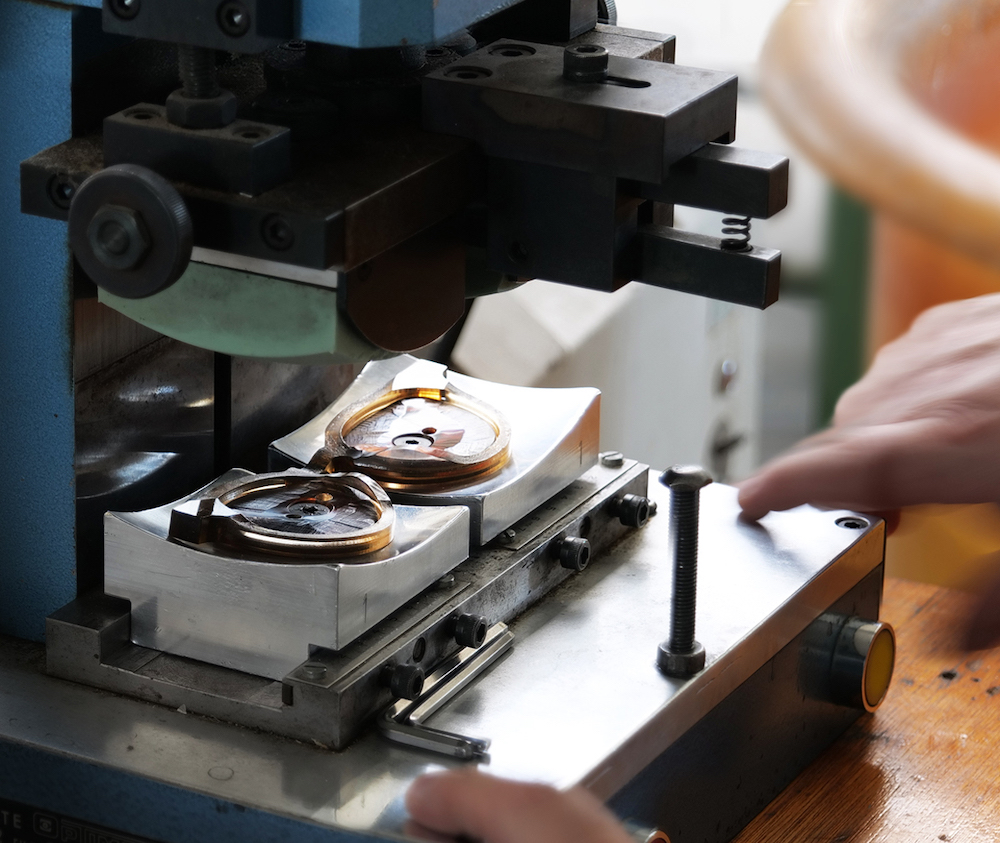
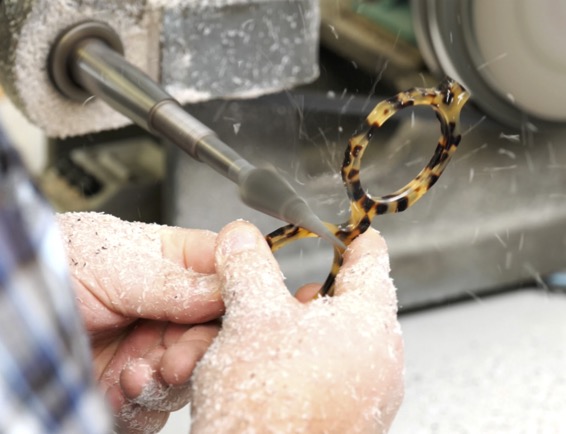
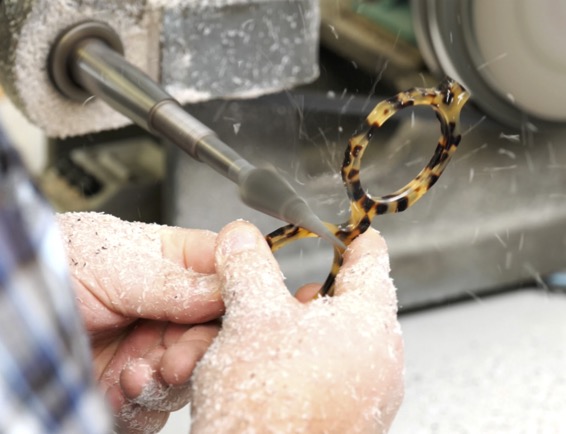


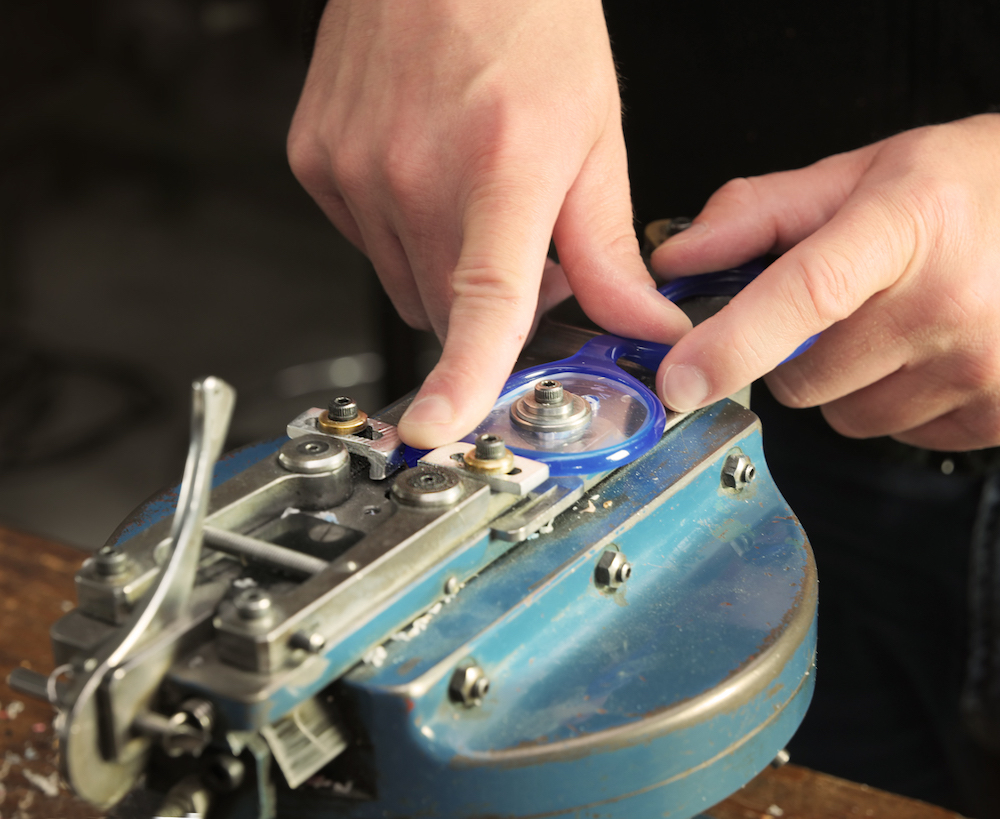
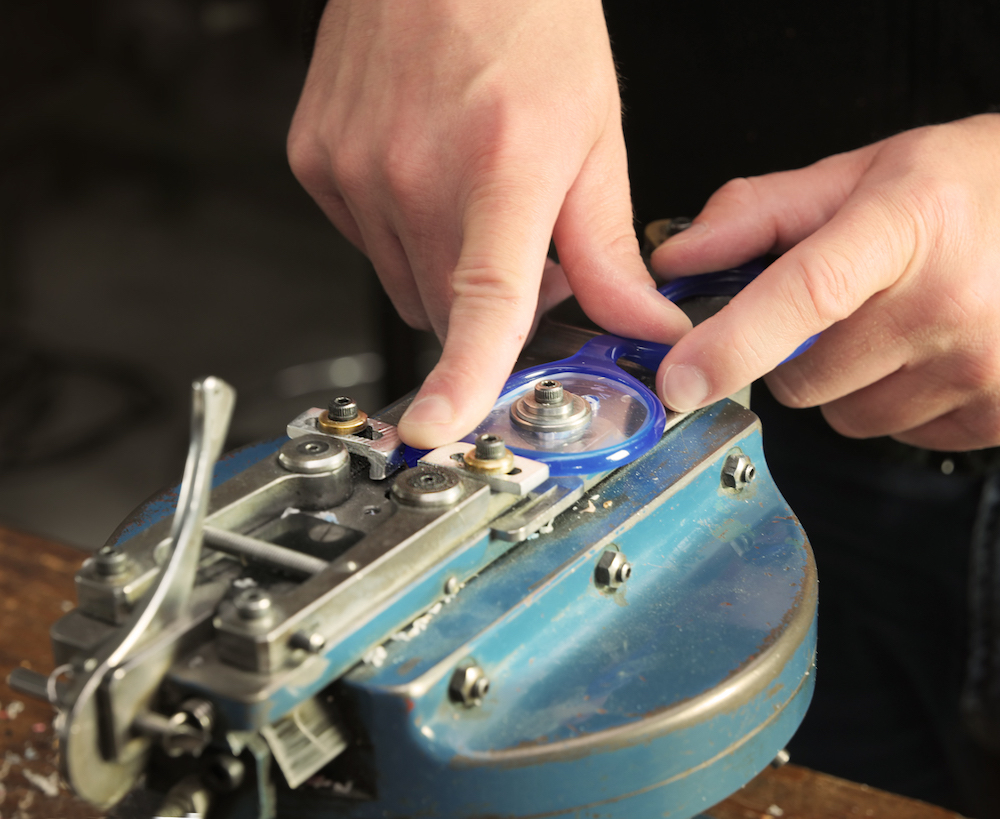
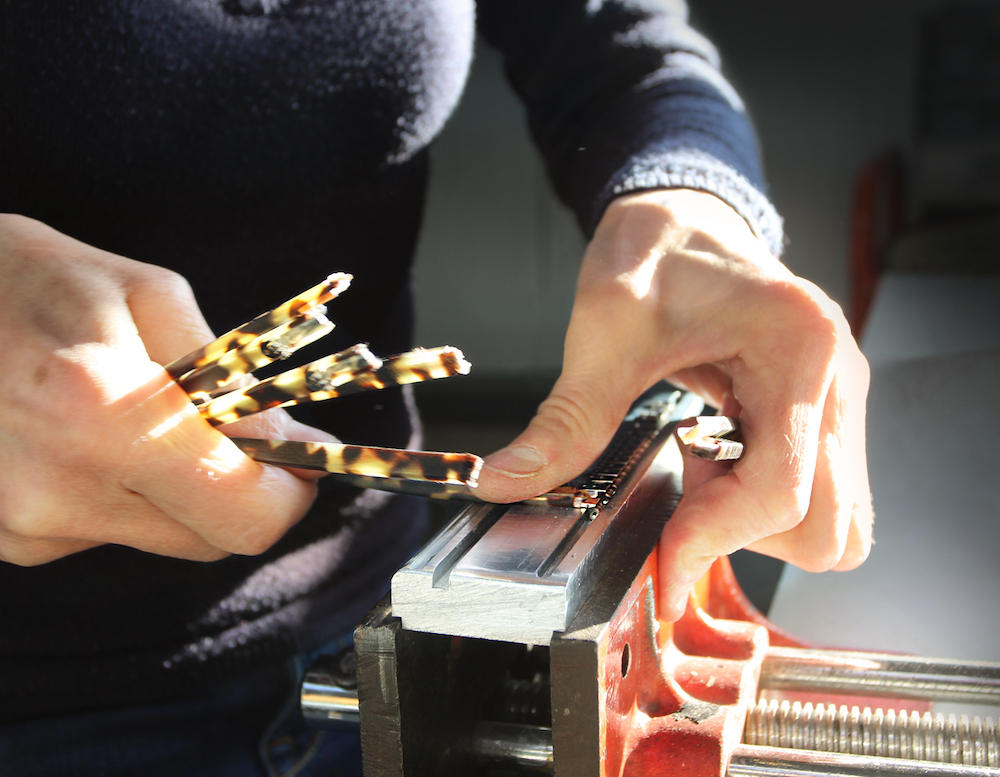
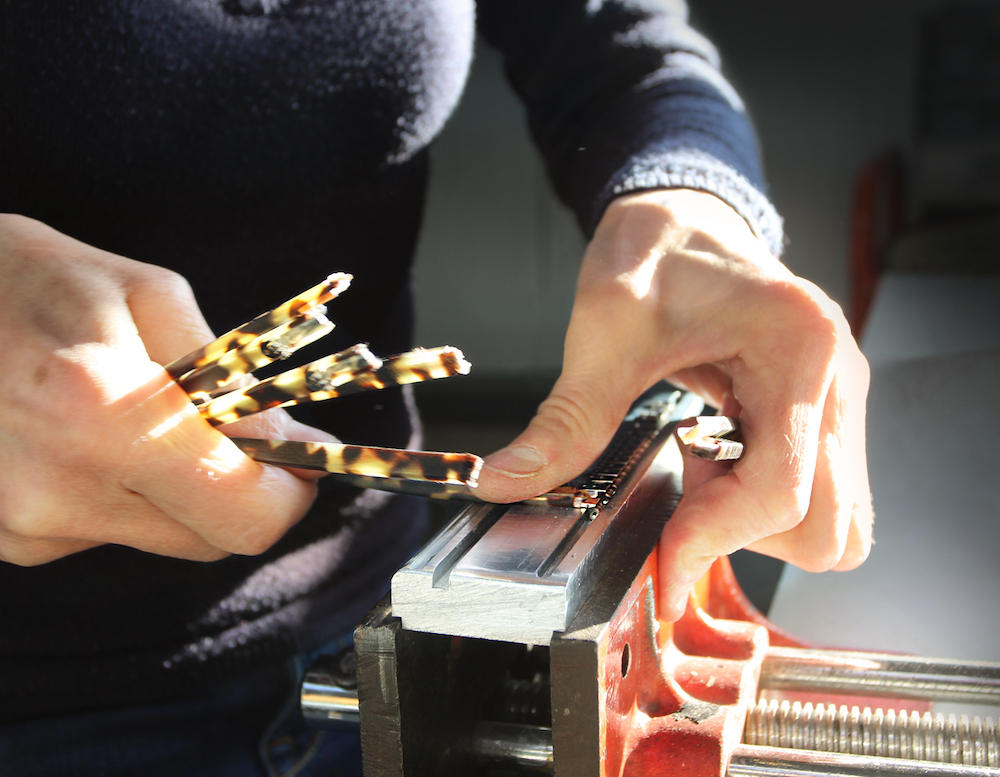
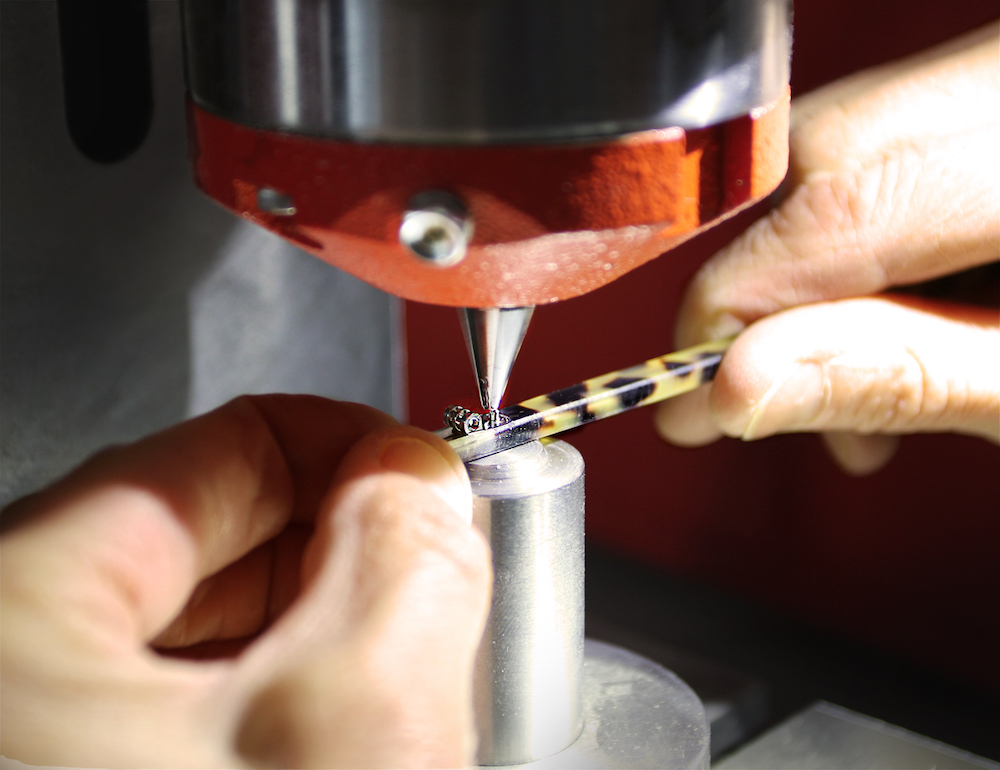
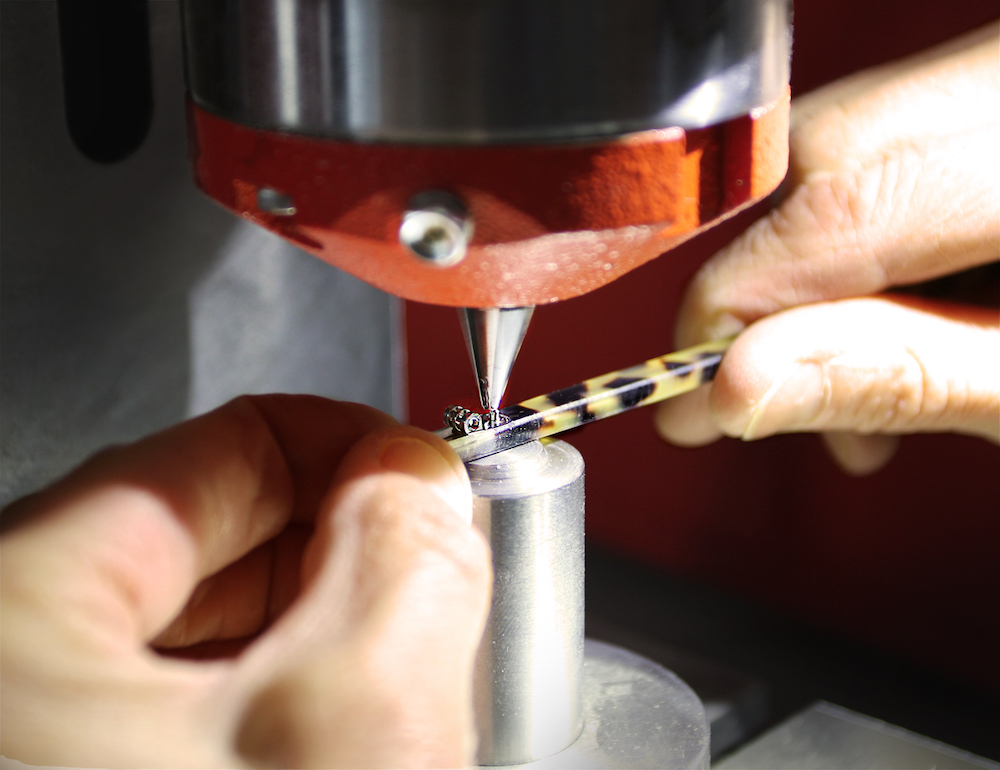
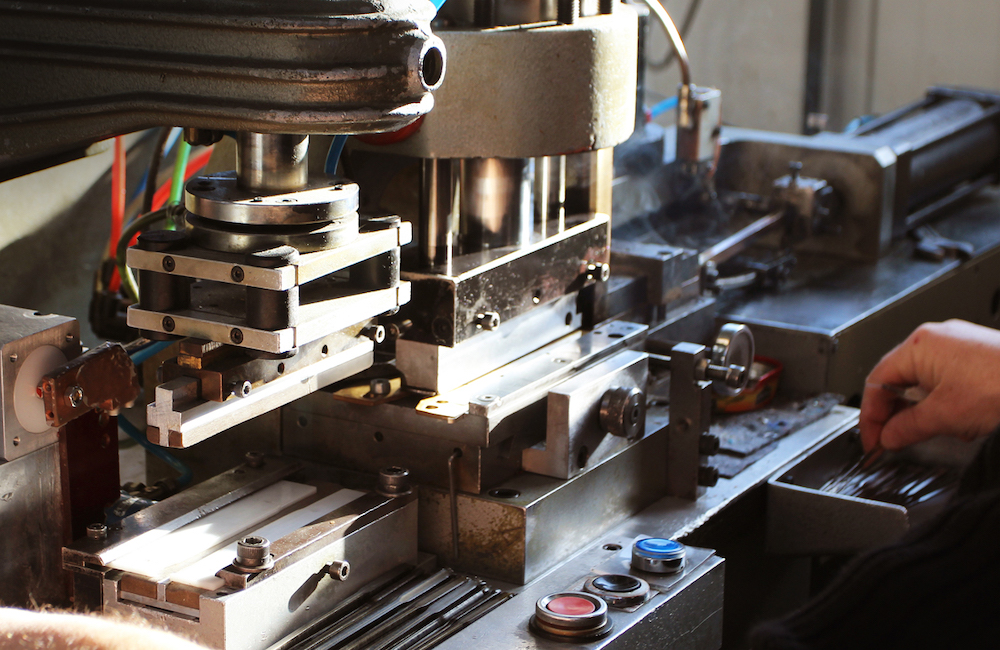
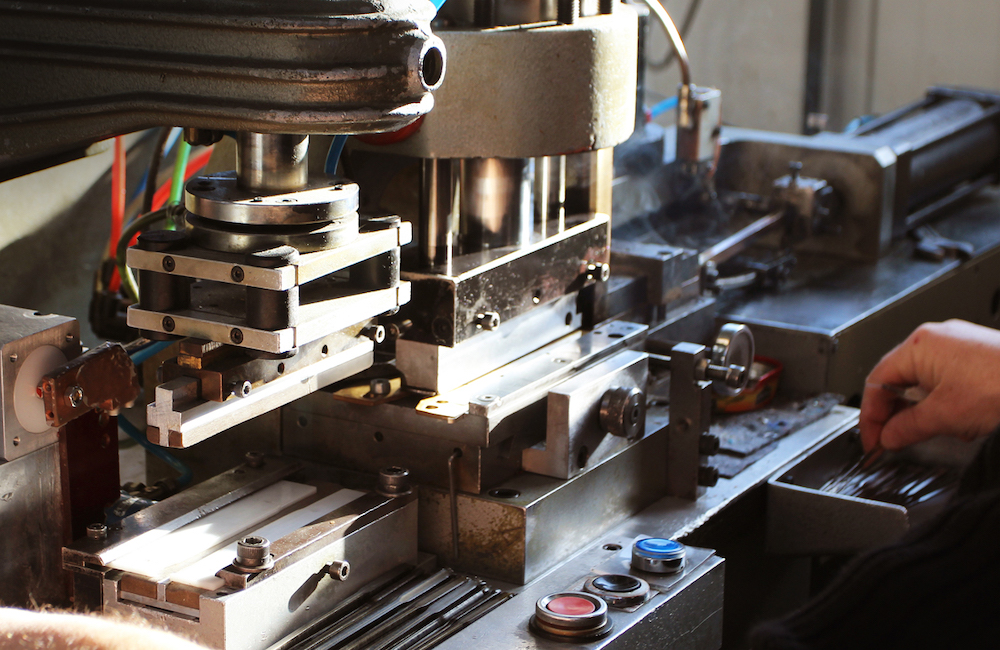
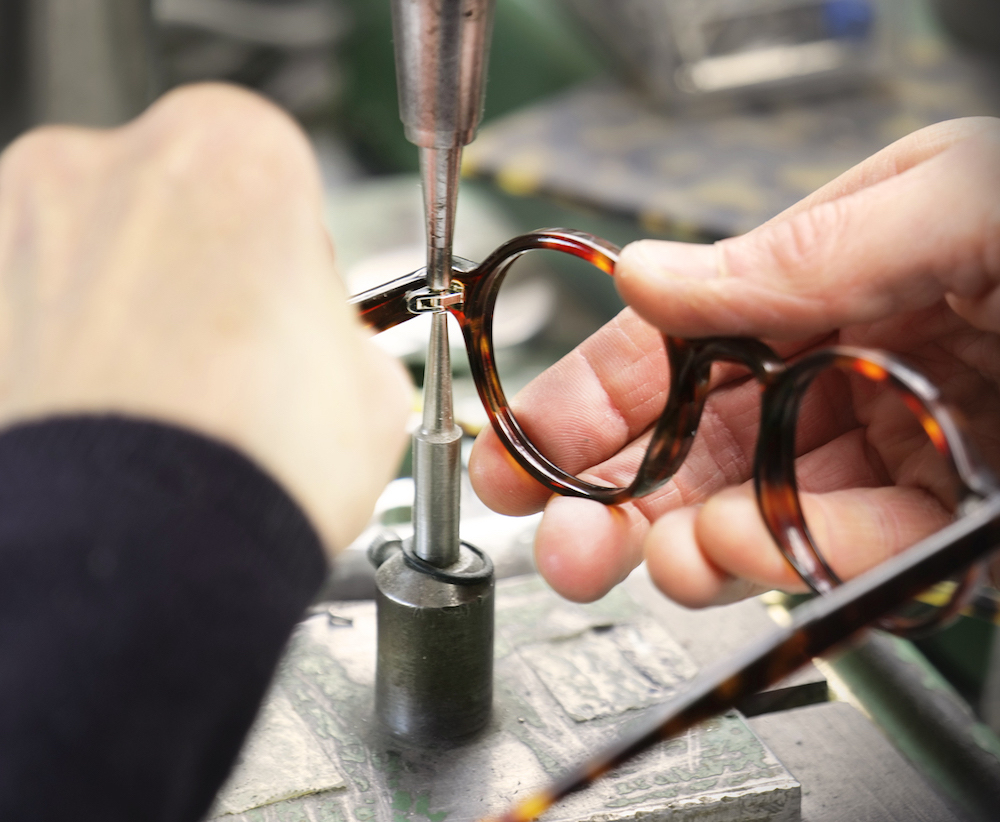
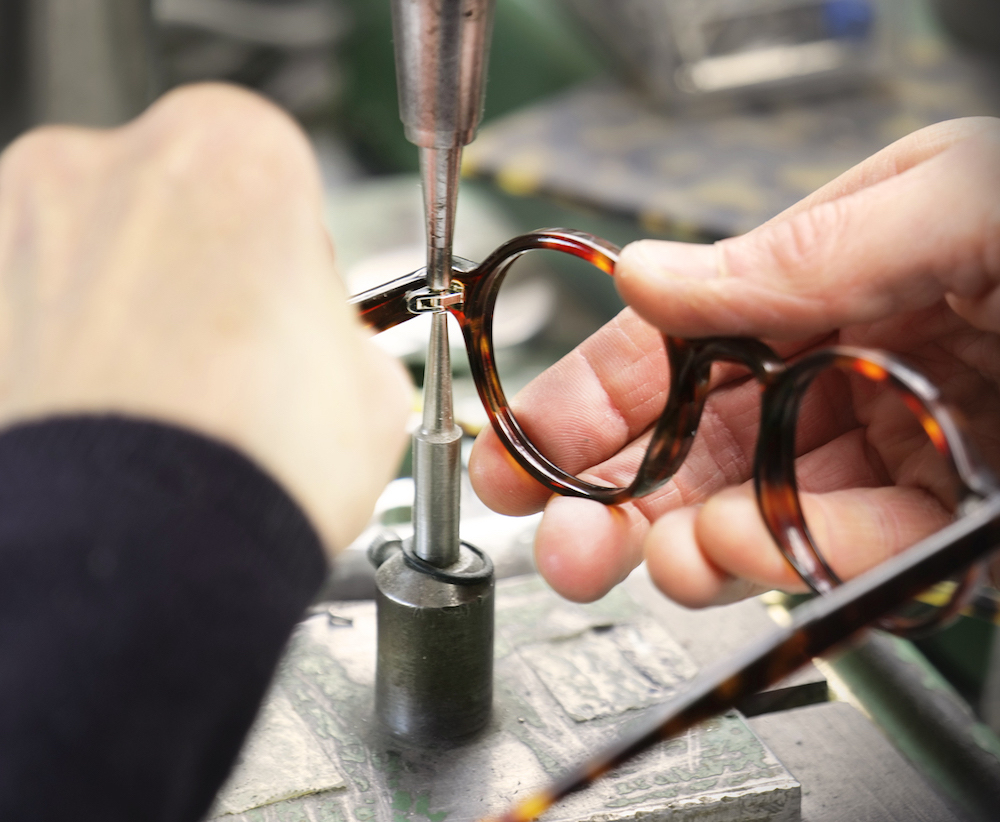
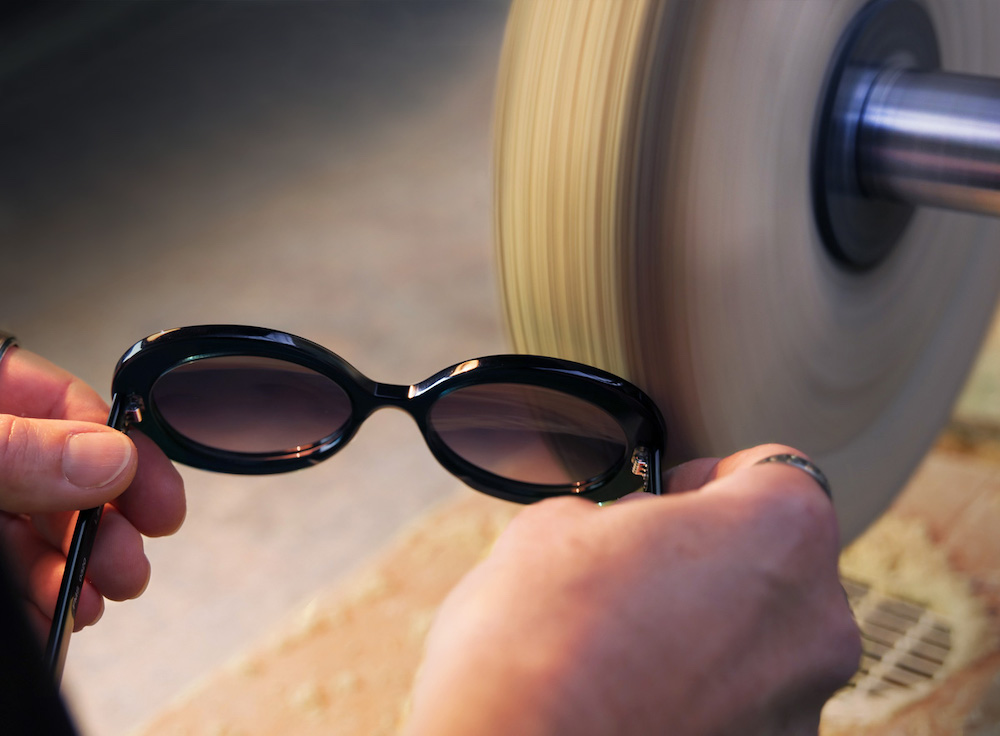
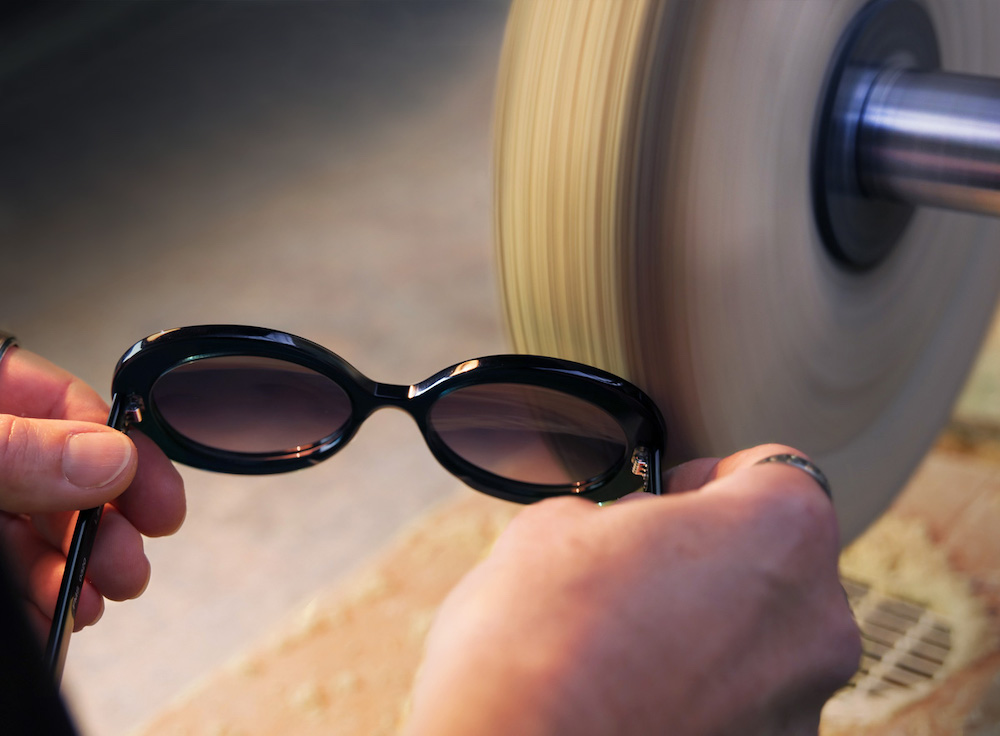